acrylic sheet (
PMMA) is a generic term for acrylic and methacrylic chemicals, commonly known as specially treated Plexiglas. In the field of plastics, acrylic refers to polymethyl methacrylate, or PMMA, which is a thermoplastic engineering plastic with excellent overall performance, and is mostly used in the form of sheets for outdoor and indoor signage. The materials in the application industry are generally in the form of particles, sheets and tubes.
1. Acrylic sheet according to the production technology is divided into casting plate and extrusion plate, transmittance is divided into transparent plate, semi-transparent plate (including dyeing plate transparent plate) performance is divided into impact plate, ultraviolet plate, color plate (including black and white and color plate), ordinary plate and special plate, such as high-impact plate, flame-retardant plate, frosted plate, metal effect plate, high wear-resistant plate, light guide plate and so on.
2. Extruded boards:Compared with casting boards, extruded boards have low molecular weight, weak mechanical properties and high softness. However, this feature is favorable for bending and thermoforming processing, and the softening time is shorter. When dealing with large-sized panels, it is conducive to a variety of faster vacuum absorption molding. At the same time, the thickness tolerance of the extruded plastic plate is less than the casting plate. Extruded board is a large number of automated production, due to the color and specifications inconvenient cooking, product specifications of the diversity of certain restrictions.
3. Casting board:High molecular weight, excellent rigidity, strength and excellent character performance. Therefore, it is suitable for processing large-size sign plaques, which take a little longer in the softening process. This type of sheet is characterized by small batch processing, unparalleled flexibility in the color system and surface texture effects, and a full range of product specifications, in a variety of special applications are practical.
4. Acrylic there is also a recycled sheet called recycled, using recycled acrylic corners, thermal decomposition to get the regenerated MMA (methyl methacrylate) monomer from the chemical polymerization reaction. After a rigorous process, you can re-obtain pure MMA monomer, and new synthetic monomer, there is no difference in quality. However, the production of decomposition monomer purity is not high, the quality and performance of the plate after molding is poor.
5. Extrusion plate using particles of raw materials, dissolved at high temperatures after extrusion molding, casting plate using MMA monomer (liquid) direct casting molding, extrusion plate shape flat and clean, but the particles of raw materials forming the completion of polymerization. Processed into a plate when the structure, performance is weak, not suitable for outdoor sign products as a material, only suitable for indoor products such as crystal text and product support. In addition, since most of the extruded boards do not have anti-violet
Outside line function, its outdoor service life is different from casting board, the color gradually fades, easy to brittle until rupture. Casting boards complete structural polymerization during the sheet processing, during which UV absorbers are added to provide extremely high strength and UV function, with an outdoor life span of more than 4 to 10 years, and the color stays bright during the period of use.
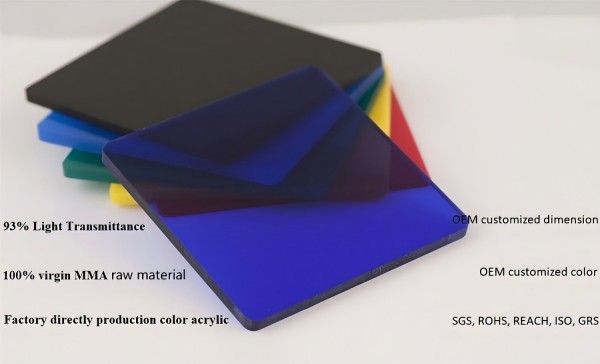
Antistatic acrylic sheet is divided into casting plate and extrusion plate:
First, acrylic extrusion plate is generally melted acrylic raw materials, high temperature extrusion with mechanical equipment.
Acrylic extrusion plate production process: acrylic raw materials → screw extruder (melting, plasticizing); → die → calendering → lamination → cutting → packaging.
Advantages of acrylic extrusion plate:
1. Suitable for single-species mass production.
2. The length of the sheet can be adjusted to produce long sheets.
3. It is easy to bend and thermoform, which is conducive to faster plastic vacuum forming of large-size plates.
4. Mass production can reduce production costs, and the scale of production has a great advantage.
Second, acrylic casting plate is made of acrylic raw materials melted at high temperatures and poured into the mold.
Acrylic casting plate production process: acrylic raw materials → heating polymerization → cooling to room temperature → poured into the template (water bath, drying room, heating) → complete polymerization → demolding → lamination → packaging.
Advantages of acrylic casting:
1. Good rigidity. (Rigidity is the ability of a material or structure to resist elastic deformation when subjected to force. It is generally understood as the ability of a material to resist external forces and maintain its original shape.)
2. Good chemical resistance.
3. Complete product specifications.
4. It has good transparency.
5. It has incomparable flexibility in color and surface texture.